Ep114: James DeMuth "Disrupting Manufacturing with Laser Printing"
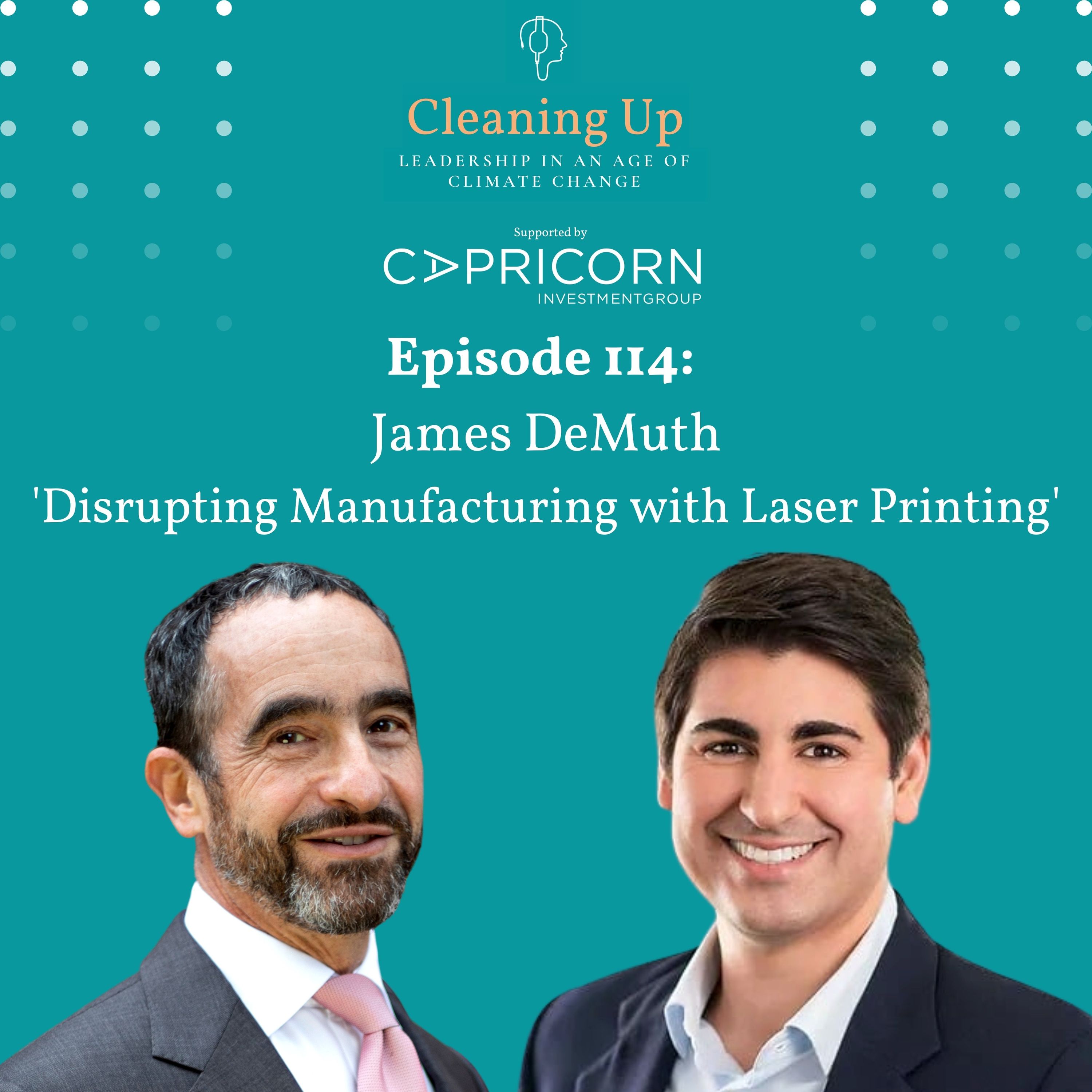
This week on Cleaning Up, Michael is joined by James DeMuth. James is co-founder and CEO of Seurat Technologies, a specialist in 3D metal printing, or Additive Manufacturing. With their own licensed laser technology, their aim is to decarbonize traditional, emissions-intensive manufacturing processes by competing with them, and ultimately, displacing them.
James is evangelical about the potential of Seurat’s technology to transform the manufacturing industry for the better:
“Our goal is to make hardware production as simple to do and as cheap to produce as it is to write code and software... I don't think we have any concept, at all, for the explosion in applications that we would see when that happens.”
Guest Bio:
Since co-founding Seurat in 2015, DeMuth has served as the company’s CTO, and as of 2020, their CEO. DeMuth spent six years at the Lawrence Livermore National Laboratory, as a Research Associate, then as a Mechanical Engineer working in Advanced Manufacturing and Fusion Energy. At LLNL, DeMuth worked on power generation, additive manufacturing technologies, and the Laser Inertial Fusion Energy (LIFE) Engine.
DeMuth holds a BSc from Santa Clara University in Mechanical Engineering, and an MA from Stanford University in Mechanical Engineering.
Edited Highlights: CLICK HERE
Relevant Guest & Topic Links:
Area Printing Explained CLICK HERE
Seurat Technologies Inc. CLICK HERE
The Economist on Seurat and Additive Manufacturing CLICK HERE
On Seurat’s 2024 plans for a 100,000-square-foot factory CLICK HERE
A comprehensive look at Seurat’s approach to additive manufacturing CLICK HERE
Why the name? CLICK HERE
Michael Liebreich James, welcome. Thank you for joining us here on Cleaning Up.
James DeMuth Michael, thank you for having me.
ML Let's get started with a little thumbnail of you, because in preparation for this, we had a little chat and it was just so fascinating and in a way relevant because of the whole kind of lasers and fusion angle. So, just give us the route, how did you get to be CEO of Seurat Technologies?
JD Sure, sure. So, you know, I've always kind of been chasing the root of problems, so to speak. Started off in grad school doing, you know, essentially robotics, for disaster recovery; found out, we need a better energy source, I went into energy; went off to Lawrence Livermore National Laboratory after my Master's at Stanford; went into essentially, how do we build a power plant from the National Ignition Facility there? We were expecting to get fusion energy any day when I joined back in 2009. Of course, what are we 12 years later, 13 years later? We finally got ignition in the recent news back in December. But, you know, we found when working on how do you turn the National Ignition Facility into a power plant, we needed advanced materials, we needed advanced design, we needed advanced geometries, we needed, essentially, new ways of making things in order to satisfy the really intense needs that the fusion environment places on structures that need to exist within it. And so, we came up with an alloy that could survive the life of the chamber, qualify for shallow land burial, all those other requirements that you need to operate in a nuclear power plant in fusion environments. But the problem was, it couldn't be welded. It had all these little oxide particles in it, that would float to the surface if you tried to weld it, and you lose all your properties. So, we looked for a whole bunch of different techniques that could process it, and one of the most promising ones was a variation of additive manufacturing called laser powder-bed fusion. And we were thrilled, it looked like, hey, we could have all of our design requirements met, we could have all the geometric requirements met, the metallurgical requirements met. The only problem was that it was gonna take over 200 years to make one of these fusion chambers using the best of the best of additive manufacturing. And, yeah, good luck with managing that project; not happening in our lifetime, for many reasons.
ML I'll let you get back to the flow of where you went next from that. But, that's just because it was so big, right? And the laser fusion process is a slow process?
JD Exactly. It's a six metre radius chamber, multiple walls, varying from a few millimeters to centimetres thick; you're just talking about a lot of metal, and laser powder-bed fusion is known for being really high quality, great geometrical tolerances, great capabilities there, but it's super slow and super expensive. We didn't even get to the cost part of it, just the slow part of it, killed that one for that purpose. But essentially, Seurat was started... I was probably in the right place at the right time; the confluence of advanced laser technology, a drive for needing to solve this problem, experts in material science, lasers, optics, all around. And, essentially we put our heads together - I'm one of five co-inventors on that initial IP - for how we essentially solve the scalability problem in additive manufacturing. And that's what we commercialized Seurat to do, to make that happen.
ML And so, the technology then you took out of Lawrence Livermore, out of the National Lab?
JD Yes. Yes. Spun it out, took a little over six months to secure a license to the technology, went out, raised a Series Seed of venture funding, a little over 3 million. Then, essentially, worked on demonstrating various prototypes and milestones along the way, raised a series A in the fall of 2017, raised our series B in June of 2021, with some follow-on money coming in the beginning of 2022. And now we're out, you know, making it happen.
ML And in my introduction, I said that one of your investors was Capricorn Investment Group, which is the supporter of this show. Which round did they come in on?
JD They came in on the series B in 2021, so they're one of our, they're a recent lead.
ML Okay, so you're now fully up and running as an additive manufacturing technology company. I just want to - before we dive into the, how wonderful, off course yours is going to be the best and the most brilliant and the cheapest, fastest and so on and the highest quality - but before we do that, I want to give people a sort of overview, a little bit, of the terrain, of additive manufacturing; why we do it, what are the different approaches. Because it's not a completely new terrain. In fact, we hear about people trying to additively print everything from biological cells to houses. Now, you don't aspire to do all of that, but maybe we can just give a bit of a thumbnail of what is... could you give a definition of additive manufacturing?
JD Yeah, I mean, at a really high level additive is... Well, it's a little bit in the name, but you're building a part up on a layer by layer process, essentially adding a new layer of material to whatever previous layer of material you've put down. And in that way, you have the ability to essentially, have almost complete freedom over whatever the next layer is. So, you can have, you basically get geometrical complexity for free. Additive has been around for a long time, especially laser-based additive, right? Originally conceived in the 1970s, first demonstrations in plastic in the 1980s, first demonstrations in metal in the early 1990s. And then, you know, patents around for about 20 years. So, you know, fast forward from 1990, to 2010, in the early 2010s, we got essentially an explosion of new additive companies coming on the market, in the field of powder-bed fusion. You had it going from one laser, to two to four to six to eight to ten to twelve or more. Over the last 10 years since then, you've had a lot of new capabilities come online, but in the whole, the technology is very, very similar to what it was initially conceived of, you know, 40 years ago. And so, there's a lot of room for potential there, improvement. And that's just on the laser side. Of course, there's the plastics... You trying to pull on that thread a little more?
ML The reason I'm sort of hesitant; I don't want to jump in because you're on a roll. But you know, you've mentioned lasers, obviously, we've got the Lawrence Livermore, and we've got the kind of laser containment, ignition, fusion thing. Now you're talking about lasers for additive manufacturing. I want to get into, why a laser helps you build something up? Because a lot of people would say, well, the laser should be kind of taking things away, you know, blasting things? We'll get back to that. But let's just touch on some of the other ways of manufacturing, there are lists out there. You must have looked at all the other ways of manufacturing when you were, you know, seeing how you could manufacture these parts for Lawrence Livermore, right? I mean, I've got polymerization, material jetting, binder jetting, extrusion, sheet lamination, deposition... Why the laser fusion? How does it beat those things?
JD Yeah, so you know, there's a lot of plastic-based techniques that are out there, which are plastics, right? And so initially, those are off the table, because we're looking to build metal chambers, right? Just to put the fusion hat back on from when I was at Livermore. Of all the techniques in metal, right, you got different types of binder jetting, you've got material jetting, you've got a variety different things where you basically... A lot of sinter-based techniques, where you lay down a layer of metal powder, and then you inject a glue, or you have essentially a metal-glue slurry that you extrude, all of those require a subsequent sintering step. And sintering, by definition means you're not melting. And so, you're never resetting the crystal structure of the metallurgy.
ML Let me do this - sorry to jump in - because my audience; I just assume my audience are really, really, really smart, but they don't know, even the little bit that I know about the difference... I'm a mechanical engineer by background, so I know what is sintering, what is melting... Can we just have it in your words? What are these sintering approaches? Because we'll get onto then why yours is different, right?
JD Yeah, so metals can have a huge wide range of properties, depending on how they're processed. And when you're talking sintering, what it really means is you have, let's say, a bunch of powder particles - imagine a bunch of little spheres all packed together - you heat them up, you get them maybe a couple 100 degrees below their melting temperature, and they start to diffuse into each other, they start to meld together. They never reach 100% density, they get close-ish. But you end up having a material that is a little hole-y, and a material that essentially is gummier, it's softer, and it doesn't have the strength that you would if you were to fully melt the material, reset the crystal structure and allow it to essentially reset itself. And so, there's only really two techniques that are out there that do that, that allow you to get the best material properties, and that's what we focused on, right? So, there's directed energy deposition, which is basically think like a big robotic welder; you got a welder on a six-axis robot, that's the simplest embodiment I can probably give for you, for a mental picture. That's something that you know, Relativity Space uses that, right, to make their rockets. It's generally characterized by low-resolution, high throughput, right? And you can get pretty good costs in the process too. But if you want higher resolution than - let's say, the size of my thumb - you need to machine the parts afterwards. And that can be extensive, it can add a lot of time, it can add a lot cost. And so, there's only so much scalability you can get to with that process. The other way you can do full-melt additive manufacturing, is by directing an energy beam to a really small spot and get melting - local melting. Essentially, you're doing micro-welding, but you're doing it really fast, and really high precision. And you can use either a laser or you can use an electron beam. But you know, electrons repel each other. And so, you can't pack as many electrons into a really small spot as you can photons into a really small spot. So, you can actually get better resolution qualities in a laser-based technique than you can in an electronic-based technique. So, that really zeroed us in to laser powder-bed fusion of all those different types.
ML What an amazing stroke of fortune, because Lawrence Livermore happens to be... What is it, they say that the L L is like Lasers Lasers?
JD [Lasers Lasers] Nothing but Lasers.
ML One of the best places in the world for lasers, and you happen to be... Or maybe it was the other way around, maybe because you knew so much about lasers, you decided that this was the leading approach?
JD Yeah, in true spirit, Livermorons would say, lasers can do anything; whether it's cutting, whether it's adding, whether it's ablating, whether it's changing colours and painting. Lasers can do it all, so why not this?
ML Ok, so now let's get on to this question of, how do lasers add, right? Because, you know, I used to read a lot of science fiction when I was a kid, and they clearly blast things up, and they destroy them. But how do they add? You were talking about, you take a metal, so you're what, taking a sort of salt shaker and shaking some salt on top of something? And then you blast it, and you melt it onto what it landed on? Is that a broad description?
ML Right? So, this is powder-bed fusion, that's the sort of, so far, so good. There's other people doing that, right?
JD That's a high-level view of it. I mean, we spread... Think of it like - this is a very simplistic view, obviously, it's a lot more precise than this - but take a pile of your salt, if you want to work with that, and you take a wiper blade from your car, and you spread it across a plate, right? Obviously, you're using much finer powder, you're using metal instead of salt, you're using a precision blade, but generally, the concept is the same. You spread a really fine layer of spherical, granular material across a build-plate, and then you come back and you hit it with a laser. And essentially you're drawing your laser like you would a colouring, book filling in a colouring book with a pen.
JD Right. There's a lot of companies doing powder-bed fusion, it's been around, again, since, basic technology since the late 1970s.
ML And therefore, I'm going to assume that the thing that spreads the particles, the hopper for the particles, the dosing, that's all standard stuff, right?
JD Um, you know, I'd say it's come a long ways, right? There is a tonne of development work that's gone on in powder-based spreading and manipulation, right? I mean, clearly, the industry has done a lot of work in that... Think granaries, right? They're dealing with powder day in and day out, but it's different. It's weird-shaped, right? And there's all sorts of stuff with the topology, and what it looks like, the size, the alloy, all of that plays into how you deal with it, and how you manage it. And so, they kind of go hand in hand. First, you want to figure out, what's the best you can spread with, then what's the best you can print with. And that might not be what you thought it was, and you iterate. So, the industry has done a lot of evolution over time. And I think there's still a tonne of potential for improvement - spreading thinner layers, more repeatable layers, faster layers, thicker layers - all of it with the needs of the system that you're working with. So, I don't think that the book is closed by any means on that development work.
ML Where I was going was not to say that the book is closed, but that that is not where... Your special sauce does not come from just being better at spreading the little granules, right? Your special sauce is coming from the lasers, right?
JD There's a strong foundation in powder spreading that we've been able to leverage and build on, but a tonne of potential as well.
ML Okay, so now tell us what your special sauce is. Okay, we've now got this powder and it's nicely spread or whatever. And you've got a laser: talk to us about your laser.
JD Yeah. So, the industry that has been around for a long time, they have one to twelve lasers or more operating, essentially focusing a laser beam down to a point that's smaller than a human hair in diameter, right? It's this really, really sharp, tiny spot. And they make a little weld pool, they weld the local powder to whatever's below it, generally the previous layer, and then they gotta do more than just the diameter of a human hair, to they start scanning it around, right? And turning it on or off as they scan it to create the pattern they're looking to create. One lasers good, two lasers are better, four better than that, eight, sixteen, you name it. But when a laser interacts with the metal powder, and it's melting it, they're trying to go as fast as possible, which means they're trying to drive the system as hard as they can in a lot of ways, which means more power, more energy, faster movement. This results in not just heating up the powder to its melting point, but heating it up to its boiling point or beyond. And like boiling water makes steam, boiling metal makes what looks like black soot. And so, they blow gas to move that soot out of the way so it doesn't interact with the laser beam because guess what: black soot absorbs laser light really, really well. And that means your laser loses intensity on the way down to the powder, and then it doesn't melt it. And so, you want to have the right intensity in the laser when you're doing your process so you have good repeatability, good reliability and so forth. And so, it's this crazy dance they have to do today, where every laser produces a soot plume from the weld pool, and every laser needs to avoid the soot plume created from every other laser. And you're doing this all within a really tight, confined volume. It gets really, really complex, really fast. And this is one of the biggest issues and barriers for scalability in the technology as it exists today, is the fact that you can't... You can crank up the power in a single beam, and you can lose resolution, right? That's directed-energy deposition, you get weld pools that are the size of your thumb. Or you can add multiple lasers, but then you have system complexity, and the system doesn't play nice, right? And so, because there's trade-offs on both, you get to diminishing returns and nonlinear math in a bad way, where one plus one doesn't equal two, it equals like one and a half. So, our insight was, we said, hey, we want to have high throughput and high resolution at the same time. And guess what, we're really familiar with lasers and how they scale, and as you grow lasers bigger and bigger, the economies of scale get better and better and better. You get nonlinear math in a fantastic way where 10x improvement in speed is like twice the cost, right? And so, you want to leverage that as much as possible. So, what we do is we generate this really giant slug of laser energy - very similar lasers to what they use at the National Ignition Facility in terms of you know, architecture, right, go figure - then what we do is the tricky part. We embed a high-resolution image into this beam. And this is probably one of the trickiest parts, because it's super hard to pattern high power lasers. Because whatever you're using to pattern it doesn't live very long: it blows up, it melts, it explodes, it combusts, you name it, right? It dies, is the end of that story. And so, how do you have a device that's incredibly efficient... because remember, every photon means more mass that's produced on the other end, and you want to produce as much as you can, for the amount of photons you're putting into the system, you want to have high efficiency. And so, you care a lot about whatever patterning device you're using absorbing very little, and it needs to survive, which also, incidentally, means it needs to absorb very little. And so, the devices that exist today don't really work for that. They have very high absorption, they have very low tolerance for high average power and high peak power; we have both. And, you know, we had the insight saying, hey, Lawrence Livermore - you know, I was there at the time, so we know what they're doing, but - they have this device that they're using for doing, essentially, dynamic beam-blocking for their high-power lasers in the National Ignition Facility for fusion, right? They have these big optics, these optics will have defects sites in them, and if those defect sites see subsequent repeated pulses of this high-power laser energy, those optics will fail, eventually, and that's bad, right? It's a huge amount of time for replacing the optics, a lot of expense. I mean these are like two foot by two foot by like six-inch-thick optics, they're massive, right? It takes a long time to fabricate them and a lot of cost. So, this dynamic beam-blocker essentially allowed, you know, the scientists at Livermore to essentially say, well, let's prevent light from ever going from that one tiny, tiny spot on the optic, which has the defect. And now that optic will never fail by that failure mechanism. And so, our insight was like, whoa, you have a dynamic beam blocker that's programmable, and it can handle really high power laser lights.... So, what if we were to use that to pattern lasers to do additive manufacturing? And that's exactly what we did.
ML Can I ask... this dynamic beam blocker: I'm a simple person, so I imagine it as like a kid's lantern, you have those shapes in front of the... So, you're stopping the laser from going through and hitting the bits that you don't want heated at that point. And coming out of Lawrence Livermore they were stopping the laser from hitting a defect, which presumably would heat up the defect and then cause failure, cracking, whatever. But what is, what is that lantern screen made of? Is it an electron beam, or is it? What is it? Give me a clue, here!
JD So it's, of course, made from crystals, because why not? No, it's a special device, it's called an optically addressed light valve. And so, it's got no internal electrodes, it's got, essentially, you have the ability to apply electric field on both sides of the device, and inside of it is essentially two big components, right? There is what's called a linear electro-optic material, i.e. liquid crystal. And there is a photoconductor, which is the layer that is activatable by a wavelength of light of our choosing. And so essentially, we project a pattern beam of low power light of that specific wavelength - in our case, it happens to be blue - and everywhere that blue light hits the device, it activates it, locally. And then that means it activates the liquid crystal, and when light passes through a liquid crystal, you can tune it in such a way that its polarization changes. And so you have, let's say, vertically polarized light coming into this, and whatever pattern you embed in this, all of a sudden, you've got that pattern in polarization space coming out, so horizontal and vertical polarizations in the pattern that you've prescribed. And you can do it really fast.
ML Again, you know, sort of correct me if I'm wrong, because I'm at the very, very limits of what I can do here, what I understand, it's kind of an optical semiconductor; you're switching it on and off, and it's either passing light through or not, based on some other pattern that you're shooting in from a slightly different direction.
JD It's like a spatial optical transistor.
ML A spatial optical transistor. You see now I can understand these words, this is good, we're getting somewhere. Now you do this... How quickly do you have to change these patterns, because you're trying to print these components really fast, you don't sit there with this thing, either just on or off, you're changing these patterns very quickly. There was another word you used, which was dynamic, right?
JD Yes. So, you know, right now, our first-generation machine is at 40 hertz. So, that means 40 times a second, that's a 25-millisecond cycle time between different sort of batches, right? Now, the transition time needs to be much faster than that. And, you know, we've got obviously, a bunch of works in the progress, our roadmap, which we talked about previously, but you know, just for our listeners here, right; I mean, we're talking going faster and faster and faster by multiple orders of magnitude and speed. And, you know, going from 40 hertz to 400 hertz to four kilohertz, right? And that means you need to go faster and faster and faster, your switching times need to speed up. And so, how we pull this in and different implementations of it... But what we're looking at is, we've qualified some stuff in the lab for extremely fast switching speeds on this, which we could potentially even be implementing now into our system, even if the overall laser isn't firing that fast. Imagine, you don't have to have just one image per shot, you could have multiple images per shot. And each image, by the way, doesn't have to be on or off, it can be grayscale. So, you can have any level of intensity in between; if you update the image multiple times during a shot, you can actually have effective heating and cooling of that powder spot, of that voxel over time, within an image. And so, every pixel can do its own heating and cooling profile. And I'm sorry if we're diving down the rabbit hole - you're a mechanical engineer by training, so I think you understand what we're talking about - but different heating and cooling rates means different material properties within your metal. Metal is hugely impacted by cooling rates, which affect crystal structure, grain orientation, surface finish, residual stress, you name it. And that means we can affect all those different levels of quality without slowing down our system.
ML Now, the thing you're trying to print is big, but the laser is working on, you know, some area of that, and then you're doing really fine work within the area of the laser, is that correct?
JD Yes. And it can all be pre-prescribed ahead of time, right? So, it's not like you're gonna do computation on the fly for that...
ML No, no, there's a program that's loaded, and then off it goes, and it works away. How big is the laser? What's the sort of diameter of the laser? You've got these pixels within the laser? Just give us an idea. I mean, are we talking about a couple of millimetres? Are we talking about a few centimetres? [inaudible]
JD Think about for steel, broadly speaking... it's material-dependent. So, aluminium would be 15 millimetres steel would be ten, tungsten might be like eight or nine, right? And so, depending on the material, you're processing and its different thermodynamic properties, you're going to see different tile sizes that we can address. And so, broadly speaking, it's around let's say, five to 15 micron pixels within the beam.
ML Okay, and then, how big are the components? And I'm going to come back to, this is all about keeping the same sort of tolerances that you can do already with the with the fusion bed deposition, but just doing it much faster. So, I'm going to ask, how big are these components? And how fast can you do them compared to the existing competitors?
JD Yeah, so what's interesting about our technology is that we don't care about what pixels are on or off within our beam. And so, it takes the same amount of time to fire a shot, right? It's a slightly different way of thinking about things, and that has pretty big implications. And so, when we're printing, it's about, just rough numbers, it's about 20 times faster for a genuine system, so just to put that out there, right, so you get that number in your head. But what we're looking at is essentially the ability to... When we say quality, we don't just mean tolerances, right, we don't just mean geometrical features. We mean all the metallurgy and dimensional properties, together. Our genuine system, we're talking 450 millimetres on a side, cubic volume, so about 18 inches. This is our starting point, and we did that just based on the system architecture and dynamics for the laser system and how it's operating. As we go to subsequent generations of machines, higher rep rates, higher energies for that laser, what we do is we keep the bed size proportional to the average power. So, the area of the bed and the average power that's coming in are roughly held constant. And so, as we look at our roadmap, right, we're looking at Gen Two system a little over a metre, maybe one to two metres on the side; Gen Three, we're talking four to six metres on the side; Gen Four for we're talking getting up towards 10 meters on a side. I mean, it starts to get, we start to get very large. But you can only really justify going big, when your production rates mean that you can print parts on a meaningful timescale for commercial needs, right?
ML Not 200 years?
JD Exactly. I mean, today, if you have a 10 metre bed, and you try and print with today's systems, it will take you, drumroll: 200 years.
ML 20 times faster is still 10 years, right? So, I'm assuming that by Gen Four...?
JD That's Gen One. So, just obviously, if we go 10x faster, for Gen Two versus Gen One, it's 10 times faster; if we go 100 times faster in Gen Three versus Gen One, that's 100 times faster, so that becomes 2000 times faster than where we are today, when we look at like the Gen Three machine. And the reason we can do this, and we can sort of have this sort of landscape of different generations is because we know how the architecture scales, from the laser side, from the machine side, and we can actually map out if you do this, this is what you'll get, and this is the economic results from that. And so...
JD The scaling between generations, you talked about, it's gonna go from 40 hertz to more hertz, right? It's gonna pulse faster. Is the laser going to get... the laser gets more powerful, presumably, it has to, right?
JD Yep. I mean, going from 40 to 400, means 10 times average power, yeah.
ML And so, Gen One, you said it's a 450 millimetre cube that you could build, If I'm following correctly, if I'm keeping up. Does Gen One exist? Have you sold some machines? Where are you in the qualification process there?
JD So, we don't sell machines. We build our machines, we build our own lasers, we build our own machines, but then we operate those machines as a contract manufacturer, right? We sell parts to customers. So, today, first step in all this is: you work with customers to qualify their alloys to all the requirements; you demonstrate repeatability and reliability in your part production; and then you scale up to series production. So right now, we are bringing our first, the Alpha revision of our general machine online. Should be running here early in 2023, early this year. We've got a prototype system that we've had on the floor that we've been able to do a lot of work on to date, but the first Alpha version of our genuine system comes online early 2023. It's the first of three machines that's in our pilot plant, our pilot plant will hold again, three machines, capable of printing about 25 metric tons of metal a year on average. And essentially, those will be... those first few machines will be the first ones to go into series production for customers, being deployed through 2023.
ML And so, you'll be... So, that was a very important distinction: you don't sell the machine, you're going to make the parts, you're gonna go to some trade show and you're gonna put a sign out saying, we can make really complicated stuff for you really cheaply with really high tolerances. What sort of trade show? What sort of stuff? Who are your customers going to be? Which sectors are you going to sell into?
JD So, interestingly, we've done zero outbound to date. We have been inundated with so much inbound demand and need from high-profile customers that, frankly, we're still just fielding inbound. And essentially our focus is looking at who we have, and identifying who should be first, right, what's the pecking order on all that? Because there's different requirements, different status, different volumes, different price points, all that stuff. And so, at this point in time, it's who's hungry, who's got the volumes; we're not looking to do prototypes, we're looking to do high volume production of mass-produced parts. You qualify the material, qualify the design, and then you make a lot of it. And the problem is, you need the price point to be low enough to be able to get to that point - if it's too high, you're ending up in really low-volume esoteric applications, like high-end automotive brake calipers, or specialty fuel injection nozzles in aerospace, right? And today, often you only hear about really high-end parts, or it's medical or aero. And what we're seeing is that, given the price points that we're enabling, we're able to expand into different markets, like consumer electronics, like automotive, and not just the highest-end cars. And in energy; energy is like aero, but on the ground, right? And so.... they have more price sensitivity than you might have for something that that needs to be up in the air.
ML And so, my impression of this piece of additive manufacturing... the very high-tolerance, you know, high quality... I guess, low-tolerance is what it really is, very accurate manufacturing in metals: it's generally used when you kind of can't make the thing any other way; you've got some internal structure, or you've got something just so complex, and the client is not that price-sensitive. Am I behind the times? Or is that accurate?
JD Yeah, so what we've found from various industry research, as we were getting going, and our sense of the market from just experience over time is that there is a lot of barriers, when you're trying to justify performance for additive, right? You're taking an application, and you're having to justify, hey, we want to use an additive approach to do this, we think we can get it to perform better. But, you know, you need to invoke a different design, you need to invoke combining, let's say multiple parts into one, you need to really pull all the benefits of additive together to justify this super high price of this really high-fidelity part. And while that's great, we think there's a better way to do things. So, when we work with customers, we say, give us your parts, we'll analyze them, we'll give you feedback on which ones we should do first, but our targets are parts that essentially, we can make cheaper, faster and more effectively than they can make it by their conventional manufacturing methods for today. And this means we immediately are able to get from the finance point of view, [get] that finance team online and excited about what we're doing without having to invoke the benefits of additive; all the benefits of additive are an afterthought, they're secondary, right? And they can be used as icing on the cake to take things to the next level. But this allows for acceleration in, essentially in qualification, acceleration in adoption.
ML In a sense, you're not competing with any of the additive manufacturing companies out there; you're going to be competing with companies doing casting and sintering, and all sorts of pretty, well... the existing - I don't want to say low tech - but the mass manufacturing technologies.
JD Exactly, and that's where the market is, right? I mean, the part market for metal parts is like two and a half trillion dollars today, growing 10% per year. And it's not in additive, it's in machining, it's in casting, and then there's some amount in forging right. And the market gets bigger as your price points get lower - go figure, right? Question is, for each of our generations of machines, where do we address... what different applications do we address where we make the right margins for the company and the business, and still give a huge advantage to our customers?
ML Do you have a kind of holy grail metric, you know, we need to get... Because there's in hydrogen, it's $1 a kilo; in solar, it was, you know, 10... Well, I always think of it as being $10 a megawatt hour. You know, when we get there, it's like, oh, the market opens up, it becomes essentially infinite.
JD Yeah, I mean, of course, we've got a ways to go, it's a big market. We've talked about this for a while: there is a fantastic price point at $25 a kilo, that, you know, that's basically the average price of a car. And that means you've gotten the automotive market, right? Or a very, very large portion of it. I think by definition, you've gotten half, right? So, we often talk about that one, but there's tonnes on the way. You look at the different industries and different volumes, there's many, many, many different sort of milestones and sweet spots. Our - probably aggressive - target is to be hitting $25 a kilo by 2030. Of course, there'll be stepping stones along the way. Our initial price is targeted at around $300 a kilo for our Gen One machine, half that for Gen Two, half that for Gen Three, and so on, right. But, again, part of this is what's the right applications, and what makes the most sense to grow the market.
ML If I take away one thing from this conversation, it will be the idea of going off to buy a car by the kilo, and saying, well, you know, I can only... I'll walk into my dealer and say I'm sorry, I can't pay more than $50 a kilo and preferably closer to $25.
JD Yeah, well, $50 a kilo, that'll get you a BMW; if you're $25, that's going to be more like your, you know, your average GMC.
ML But let's say you've got the Gen One and you're at $300 a kilo, just give us an idea of a couple of, off the top your head, a couple of the types of parts. Whether it's for car or anything else, what are we talking about here in consumer electronics or in energy, or in automotive? What type of part would it be?
JD Yeah, I mean, there's a whole variety, right? I mean, for energy generation, you're talking various aspects of parts that were previously cast, and then machined. In pretty much all these industries, they were cast and then machined. They might have been cold-rolled, and then machined, but generally, it's a multi-component process. So, you've got turbine blades, you've got compressor wheels, you've got wearable housings, you've got cellular phones, you've got a whole slew of different components that I think are broadly in those veins. You've got a lot of, oddly enough, plumbing parts, you've got manifolds, things that were... They could get very complex, there's benefits to it. I mean, obviously, we're not going to not take the markets that additive exists in today. The problem with the markets that additive exists in today is they're small, right? They're low volume, they're not high-volume production. And so, it's kind of marrying the two, it's taking the benefits of additive to that next-level market that I think we're primed to and poised to do.
ML So, there's a whole range of different things that I'm imagining - as I say, I'm a mechanical engineering - there's valve housings and all sorts of stuff that I could see that this could really... The combination of volume and price point, I can see how you can munch your way through that over time. One question I want to just come back to briefly is, why not just sell the machines? I mean, if you're going to be really good at the technology of the machines, why do you want to get into that customer service? Customers are a real pain, let me tell you. You know, you have to qualify things, you have to work with their design teams, it takes years, why do that? Why not just sell the machines? These are presumably quite expensive, right?
JD Yeah, so there's a number of reasons for that, right? I mean, you're talking sales cycle. Selling machine in a sales cycle is much, much longer than selling a part, because the customer also has to qualify the part on their end. You still have to do the part qualification either way you go, you can't get away from that. And so, when you're selling a machine, you got that embedded in it, plus the high price of the machine and the sales cycle. Our trajectory, our roadmap: we often say know you want to be when you grow up, right? When we grow up, our machines are getting bigger and bigger and bigger, and more and more and more expensive, which means a longer and longer and longer sales cycle and less customers who can actually afford to purchase them. There's still a huge market for customers that are, wanting mid-size batches and not just you know, exorbitantly high batches of volumes of parts. And so, that's another part of the equation in there. When we look at selling parts, there's not many customers who are going to be able to buy a half a billion-dollar machine, fast forward a decade or so, right? But everyone's gonna want to buy parts at $25 a kilo.
ML Although, if you look at analogies from other industries - it might be the wafer fab business, the fab business in semiconductors - you do tend to get specialists who produce the machines and then, you know, a half a billion machine, if you're just making, I don't know, you're making valves or you're making turbo charges, you don't want to spend that. But on the other hand, going to a specialist contract manufacturer, who has got the balance sheet and the capability to buy a machine for half a billion dollars, and then run it. You would see yourself as not going that route, but actually continuing to own and manage those machines?
JD So, I think it comes down to what do customers want at the end of the day? Customers don't want a machine, customers want parts.
ML Well, if a customer is a contract manufacturer, they might want a machine, right, because it gives them something else they can make?
JD But that's not... I mean it depends on what market you're in, right? Those aren't our customers today, right? Our customers are the people who are producing parts, because that's, at the end of the day, the whole point of the machine is not to be a machine, it's to produce parts. We get the best strategic and incentivized alignment with our customers when our machines are as primed and as tuned as best as possible to deliver quality in the parts. And there's such a wide spectrum of parts and materials out there, that there's going to be no end to the discovery that's going to happen for how you can print parts better, and the modifications that will be necessary on the machine in order to do that. And we see the longest-term potential here for us is to be intimately tied into that process, to be able to understand the outputs, feed it back into the inputs, and ultimately deliver the best possible solution to our customers, which we would not have the insight into if we were just doing machine sales.
ML Okay, there is an implication - I mean, to use your figure - you said these machines, [are] half a billion dollars each: how many of these machines are you going to be running in ten years and who are your investment bankers, because they're gonna love you?
JD They will! There's a lot of money out there that's just looking for a good way to get put to work. And we're happy, we're so happy to provide that avenue and access to make that money make a return on investment. I mean, broadly speaking, we deploy a part-printing factory, we're looking at just a few years for payback on that investment. So, the economics are very, very attractive, when we're talking about how we're deploying our part-printing factories to deliver goods for our customers.
ML James, I've got a final little set of questions that I want to ask you, which is: this is all fascinating - I mean, I have the mechanical engineering background, so I absolutely love what you're doing, it's tremendous - but, this is a show about leadership in the age of climate change climate action, environmental [issues.] How does this help save the world, the planet?
JD Yeah, why am I on this call? No, I'm just kidding. So, we are, effectively, electrifying manufacturing, right? We're taking a manufacturing industry, which has been powered for eons, effectively - you know, casting has been around for thousands of years - we're taking an industry that has been driven by fossil fuels forever, and [we're] turning into one that can be energy source agnostic, right? Casting makes up 20% of the global manufacturing market for metal parts. Machining, another example, right, machining makes up about 45%. So, subtractive manufacturing, you take a mill, you take a lathe, you're cutting away material on your part. Most parts that are machined, you're machining 60 to 80% of your starting feedstock material away, and that's material that never need be made in the first place. Now, you can either have less material made in the first place, which means less emissions, or you can have just more parts made in general, which means more production, which means... Those parts are being made for a reason to benefit society, right? So, either way you go, your amount of emissions per part made, there's a huge potential to do that better. And we see a huge opportunity to enable that potential through our process of what we call area printing. Of course, there's all sorts of other effects, like... Our vision is, you have a part-printing factory deployed at our customer's site, making parts on demand for customers where they're needed, when they're needed, which means great reductions in supply chain complexity; I think we've all been very painfully aware of all the issues with our supply chain over the last couple of years. So, how can we have parts made locally, reshore manufacturing, wherever your shore might be. We're obviously very US-focused and centric, based on our technology, a spin-out from a national lab. But I think... this is a global problem. This is a problem that is pervasive throughout the world, right? Getting parts from A to B, that are made half the world away - why? Let's make them locally. Let's boost our local economies, let's make that happen, and generally, it's economics that don't allow you to do that, or that incentivize it to be done elsewhere, and we're able to change the paradigm, and make it made locally. There's warehousing reduction, and so forth. There's a whole list of different ways where we can impact, directly, emissions. Then you get into the secondary impacts, and this is literally unlimited. You know, you talk about saying, hey, I'm going to take a car, I'm gonna take away 10%, 20%, 30%, 40%, of the mass; that means it takes that percent less energy roughly to move it from A to B. You can talk about energy generation, right? I'm going to make my turbine blades more efficient so they can operate at higher temperature; I get my overall turbine at a higher efficiency. That means I get more energy out per fuel in. You're talking about enabling new technologies like fusion, right? You're talking about all these different things that are possible because you've leveraged the benefits of additive, done weight reduction, you've done performance enhancement, and so forth. And right now, we talked earlier about, hey, there's all these benefits of additive, you know, we don't want to invoke them yadda, yadda, yadda. But you invoked them; today, they're being invoked because they need to be invoked from a cost perspective. Well, that means they're only being invoked for a very small sliver of parts. What if they could be invoked for all parts? And now you suddenly have unlocked design freedom for literally every part that can be made. Everything that's, from our technology perspective, a meltable material: metals, glass, plastics, ceramics. Anything that melts has the potential to be enabled by this. You've dropped the price point of all that to something where, essentially, you're seeing pervasive use of this freedom of design; I don't think we have any concept, at all, for the explosion in applications that we would see when that happens. And frankly, that's probably one of the things I'm most excited about - where do we go? You can make steel, a steel structure with an embedded structure within it, lighter, stiffer than carbon fibre, but infinitely recyclable. No fatigue limit, unlike aluminium, right? It can have high temperature-withstanding properties, it's got all the properties of steel, but it's behaving like a different material, right? These are all the things that you can do when you can start talking about embedded structures, metamaterials, materials that don't behave like anything that's in existence today, and you have the freedom of design on top of it! Our goal is to kind of make hardware production as simple to do and as cheap to produce as it is to write code and software. And when you can do that, there's gonna be an explosion of capabilities. Energy is going to be a big one that's impacted by it, and emissions, and efficiency. But I think we're gonna see a load of others as well.
ML That was an extraordinary sort of, evangelical section, for what this technology can do, and very persuasive. You know, I'm a sort of prosaic guy, so I'm just thinking, well, what you're really talking about is that break caliper that right now, you can only afford on a on a high-end Porsche, is suddenly going to be available for the low-end car. All of the above for $25 a kilo, that's going to be transformational. It's very exciting.
JD Exactly. You know, we don't just want the Bugatti brake caliper, we want the Honda Civic or the Ford Focus brake caliper, right?
ML And presumably, you can do all of the sort of surface treatments and so on, in the same passes with the same laser? So, you can harden, and you can do all that kind of stuff, integrated at the same time?
JD Lasers can do a lot of things. Yeah, I have to make my colleagues at Livermore proud, right? Lasers, lasers, nothing but lasers. Sorry.
ML L L N B L? Lawrence Livermore National...
JD There's LLNL, which is Lawrence Livermore National Laboratory and Lawrence Berkeley National Laboratory.
ML OK, so it's lasers, lasers, nothing but lasers. But there is one... I have out there in my audience also some people who think that we should not be.... the way to solve climate is to consume less, we should de-grow, we should just do less. And they'll probably be excited by the idea that you can do things more efficiently, but they might be scared that if you do all these wonderful things for $25 a kilo, that we're going to buy more cars, and we're going to make more of everything because it's just become so cheap. And so, there'll be what they call a rebound effect, and this won't help the planet at all. Do you worry about that?
JD I think if the rebound effect is coming, still leveraging greenhouse gas emitting fossil fuels, and you're making more of it, yeah, you don't want to go in that direction. But you do want to go in the direction where... I mean, I don't think we're going to be as a society going less in terms of energy consumption, I just think we need to have better sources of energy that can get us to where we need to be, but do so in a sustainable way, right? We are right now not living in harmony with the world, right? We're not living in a sustainable point of view, with how things are going on, right? We're changing things, and we need to figure out how we can live sustainably. I don't think that necessarily says we need to do less, I just think we need to do different. And I think that we can have both, but we need to be smart about it. So, it's not easy, but I think there's lots of paths out there. And how do we grow this future? I think it's like how do you eat an elephant, right? One bite at a time, you just need to have the right direction.
ML You're talking my language: this is, continued human progress, continued standard of living improvements, continued health improvements, education, etc., etc., but decoupled from the physical impact of what we're doing on the planet. So, on that note, I would love to just thank you for the time you've spent with us, it is an inspiring story, it's a great technology. direction. I wish you enormous luck in hitting your Gen One, Gen Two, Gen Three, Gen Four. And I'm sure that my audience will have enjoyed it as much as I have.
JD Terrific, Michael, well, thank you for having me today, it was wonderful to be here with you, and hopefully we can come back someday.